
PROBLEMS WE SOLVE
DEEP UNDERSTANDING LEADS TO APPROPRIATE SOLUTIONS

We solve different types of problems on mechanisms and assemblies, from microvibrations to bearing failure.
We also bring our skills and expertise to the optimal engineering of new solutions, even in extreme conditions of speed and/or loads.
​
We have application engineering AND innovative product engineering capabilities.
​
See selection of project example below.
Under certain conditions, the cage of a ball bearing (also called retainer or separator) may exhibit erratic movement or cage whirl. This is particularly the case for poorly lubricated or heavily stressed bearings. In the event of such dynamic instability (or bearing squeal), the energy exchanges involved can lead to cage rupture. This is a common problem with turbopumps or with the reaction wheels of space probes or satellites, which can result in an unwanted change or termination of the mission. This is also a problem encountered in the spindles of machine tools for example.
Although this phenomenon has been studied for more than 50 years, it had not been fully modelled or solved…
Until recently. We did it with the BUTTERFLY Cage.
​
​
​
​
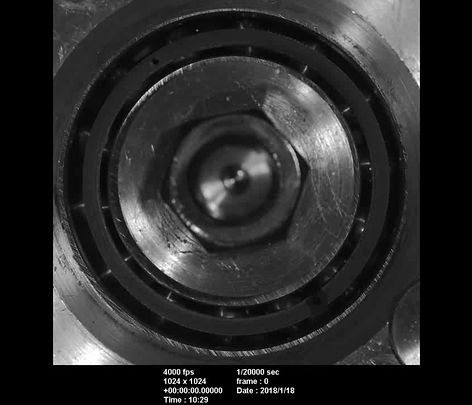
cage instability
Cage instability phenomenon - Videos Courtesy of ESA/ESTL (ESR Technology, UK)
​
STABILITY MAPS
Drawing on a unique worldwide methodology based on the STABILITY MAPS concept, we can accurately assess any cage's sensitivity to the risk of instability.
Other problems we solve:
​
​
​
A lot of industrial applications imply that the relative rotation of the rings of a ball bearing is accompanied by a combination of axial and radial loads.
Those miscellaneously loaded bearings induce misalignment of the rings that leads to the Ball Speed Variation phenomenon (ball advance at non-constant speed). This phenomenon can lead to cage failure, noise, vibrations, and excessive heat.
.
Current available bearings only provide a partial answer to this problem. Deep groove and angular ball bearings can indeed only tolerate a small amount of misalignment, roller bearings must also respect a perfect alignment of the rings, and self-aligning bearings, if they can tolerate more significant misalignment, cannot support axial loads due to the outer ring geometry.
​
After decades during which the designers of mechanisms had to accept difficult compromises, APO-GEE offers them a solution which opens up new perspectives: the COBWEB Bearing (patent drafting ongoing). The design of this new Cobweb bearing significantly decreases the negative effect of the misalignment. It is capable of supporting a combination of axial and radial loads, exactly as deep groove and angular bearings but with a considerably extended acceptable misalignment.
​
Yes, we have engineered the bearing that has the most precise functioning in the world.
​
​
​
Friction at the contact between the balls and the races induces significant heating and energy dissipation.
​
In some situations, the heat produced cannot be properly evacuated and leads to thermal instability of the ball bearing, resulting in the loss of the ball bearing.
​
​
At very high rotation speed, the bearing may lose some of its stiffness. Since the bearing is the link between the shaft it supports and the rest of the mechanical assembly, the exact calculation of stiffness is fundamental to ensure the proper functioning of the assembly.
While finite element design methods are commonly used to design rotating machines and describe vibrations, they are ineffective in modelling bearing stiffness.
​
​
Poor design of the bearing may lead to premature bearing failure.
Depending on the functionality of the mechanical component in which the bearing fits, a trade-off must be found between mechanical strength and dissipated power.
​
​

BALL SPEED VARIATION
THERMAL INSTABILITY
BEARING STIFFNESS
INCORRECT BEARING design
SELECTED PROJECT EXAMPLES
At APO-GEE, we partner with top-tier companies across the aerospace, defense, automotive, spindles and other industrial sectors to solve complex bearing-related challenges. We save customers time, eliminate costly, intensive research, prevent possible disasters and reduce the risk associated with poor design.
Below is a selection of real-world projects we’ve worked on, each one demonstrating how our expertise in bearing behavior, failure diagnosis, and custom solutions can directly support your mechanisms reliability and performance goals.
​
-
Clear performance diagnosis on space-grade bearings in one of the most advanced instruments ever launched into orbit, ensuring long-term functionality in extreme conditions.
-
Root cause analysis of cage failure in cryogenic defense equipment, followed by the design of a tailored solution adapted to operating conditions.
-
Determining optimal bearing solutions for a critical new defense system, under severe mechanical and operational constraints, helping ensure system durability and compliance.
-
Diagnosing vibration issues in turbochargers.
-
Improving bearing reliability in compressors by analyzing failure modes and implementing design adjustments, significantly increasing operational lifespan.
-
Addressing bearing reliability issues in high-precision therapeutic equipment for tumor treatment, reducing downtime and maintenance costs.
-
Identifying cage instability in a turbomolecular pump, with a view to restore full operational stability under demanding vacuum conditions.
-
Analyzing complex cage dynamics across multiple bearing types to isolate the root cause of rattling noise in high-speed spindles, leading to a proven design fix.
-
Deploying our proprietary Butterfly Cage technology in spindle bearings to fully eliminate rattling noise and minimize vibration signatures.
-
Diagnosing cage instability in marine stabilizer mechanisms, enabling to improve reliability and reduce customer complaints.
-
Advising on bearing definition approach for rocket engine turbopumps, ensuring optimal performance under extreme load and thermal environments for New Space propulsion developers.
-
Solving cage instability in control moment gyroscopes for satellites using upgraded COTS bearings with Butterfly cages.
-
Supporting a Tier 2 automotive supplier in identifying and mitigating cage design flaws.
-
Implementing an innovative, predictive diagnostic method for cage instability in Reaction Wheel Assemblies (RWAs) and gyroscope bearings, used in multiple space programs.
-
…​
​
Whether you're launching into orbit, racing at 100.000 rpm, or operating under demanding industrial constraint, APO-GEE brings deep expertise, proven problem-solving methods, and concrete innovative products to your most critical bearing challenges.
​